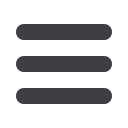
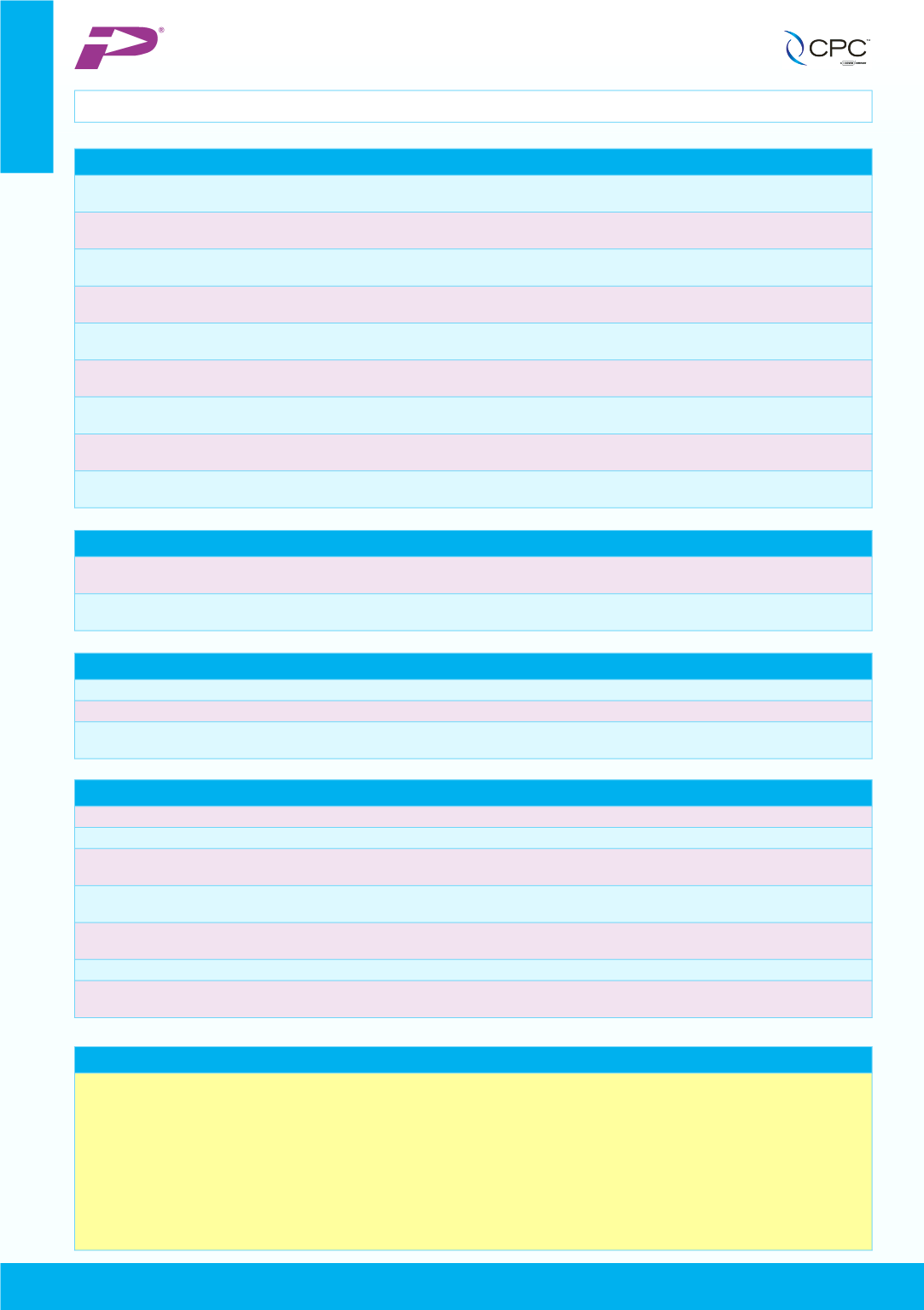
110
Two
MATERIAL OPTIONS
The type of media flowing through a connection can affect the strength, surface appearance, colour, and performance of the connection. Some guidelines for
the different types of material:
THERMOPLASTICS
Acetal
Strong, lightweight and economical and is used for a wide variety of chemical and mechanical components. Acetal offers high strength and rigidity over
a broad temperature range, low wear, toughness and resistance to repeated use.
ABS
Economical medical-grade thermoplastic that withstands gamma and e-beam sterilisation. It is commonly used in medical devices. ABS is an amorphous
material with good physical properties and high resistance to chemical attack.
Polyamide
(Nylon)
Very resistant to wear and abrasion, good mechanical properties even at elevated temperatures, low permeability to gases and good
chemical resistance.
Polysulfone
Rigid material with excellent strength, good chemical resistance, withstands repeated sterilisation, and higher temperatures than other
thermoplastics. High hydrolytic stability allows it’s use in medical applications requiring autoclave and steam sterilisation.
Polycarbonate
Resistant to some chemicals, withstands sterilisation and is transparent. It is commonly used in medical devices and offers impact resistance,
outstanding dimensional stability and good optical properties.
Polypropylene
Excellent general purpose resin that is highly resistant to chemical attack from solvents and chemicals in harsh environments. In general,
polypropylene is resistant to environmental stress cracking, and it can be exposed to challenging environments.
Polyethylene
Low-cost, chemically resistant thermoplastic. It is opaque, and can withstand reasonably high temperature. Polyethylene, unlike polypropylene,
cannot withstand normally required autoclaving conditions.
PEEK
(Polyetheretherketon)
Highly temperature resistant, engineered thermoplastic with excellent chemical and fatigue resistance. It exhibits superior
mechanical and electrical properties.
PPS
(Polyethylene Sulfide)
Broadest resistance to chemicals for its market as an advanced engineering plastic. (PEEK and PTFE have better resistance,
but are not considered engineering resins.)
FLUOROPOLYMERS
PVDF
Tough engineering thermoplastic with a balance of physical and chemical properties that qualify it for high performance in a wide range of applications.
It is mechanically strong and tough, has good ductility, and has a broad, useful temperature range.
PTFE
Chemically resistant to all chemicals and solvents with the exception of some molten metals, molten sodium hydroxide, elemental fluorine, and certain
fluorinating agents. PTFE offers chemical resistance and stability at high temperature.
ALLOYS
Chrome-plated brass
Rugged metallic material with an attractive appearance, chrome-plated brass is excellent for higher pressure and temperature.
Die-cast zinc
Durable and lightweight (about 20% less than comparable brass) material that withstands high pressure and temperature.
Aluminium
Lightweight metal with an available hard anodized finish for durability. Aluminium is non-toxic, non-magnetic and non-sparking and is known for
its high strength to weight ratio.
O-RING SELECTION
Buna-N
A common material for o-rings with a temperature range of -4°C to 121°C (-30°F to 250°F).
FKM
Well known for its outstanding resistance to heat, oxidation, weathering, and ozone. The temperature range is -26°C to 204°C (-15°F to 400°F).
EPDM
Ethylene-propylene-diene rubber (EPDM, also sometimes referred to as EPR) is a chemically resistant family of compounds. Colder uses high quality
peroxide cured EPDMs that provide exceptional resistance to temperatures with a wide range of chemicals.
FFKM
(Chemraz®, Simriz®, Kalrez®)
Broadest range of chemical resistance of any elastomeric material, combining the resilience and sealing force of
an elastomer with chemical resistance approaching that of PTFE.
PFA & FEP
Encapsulated seals combine the resiliency of the elastomer with the superior chemical resistance of the fluoropolymer to achieve a seal that is
lower cost than a pure fluoroelastomer FFKM seal.
Food-grade
Commonly used when food, beverages or potable water is going through the coupling.
Silicone
Seals have good temperature resistance. The temperature range is -57°C to 204°C (-70°F to 400°F) with special compounds that can reach 79°C to
232°C (175°F to 450°F). Silicone can also be supplied with Class VI requirements for life sciences applications.
INTERPRETATION OF TEST DATA
WARNING:
The compatibility data was assembled from 3 main sources: a) the Chemical Resistance Guides published by COMPASS PUBLICATIONS
©
, b) the Chemical
Resistance guide published by VICTREX, the manufacturer of PEEK
™
and c) the Entegris Chemical Compatibility Chart. The table is to be used as a
general guide only. Colder Products Company is not responsible for the accuracy of this data and assumes no obligation of liability in connection with its use.
Therefore, CPC insists that all customers test and evaluate the suitability for use of CPC couplings in their particular application before using the
couplings.
NOTES:
* PVDF may discolour after prolonged exposure in Potassium Hydroxide.
* Polypropylene may discolour after prolonged exposure in Sulfuric Acid.
Viton
®
is a registered trademark of Dupont Dow Elastomers, PEEK
™
is a trademark of Victrex USA, Inc, Halar
®
is a registered trademark of Ausimont,
Chemraz
®
is a registered trademark of Green Tweed.